鍛造コストを抑える方法とは?効果的な鍛造費用削減のポイント5つ
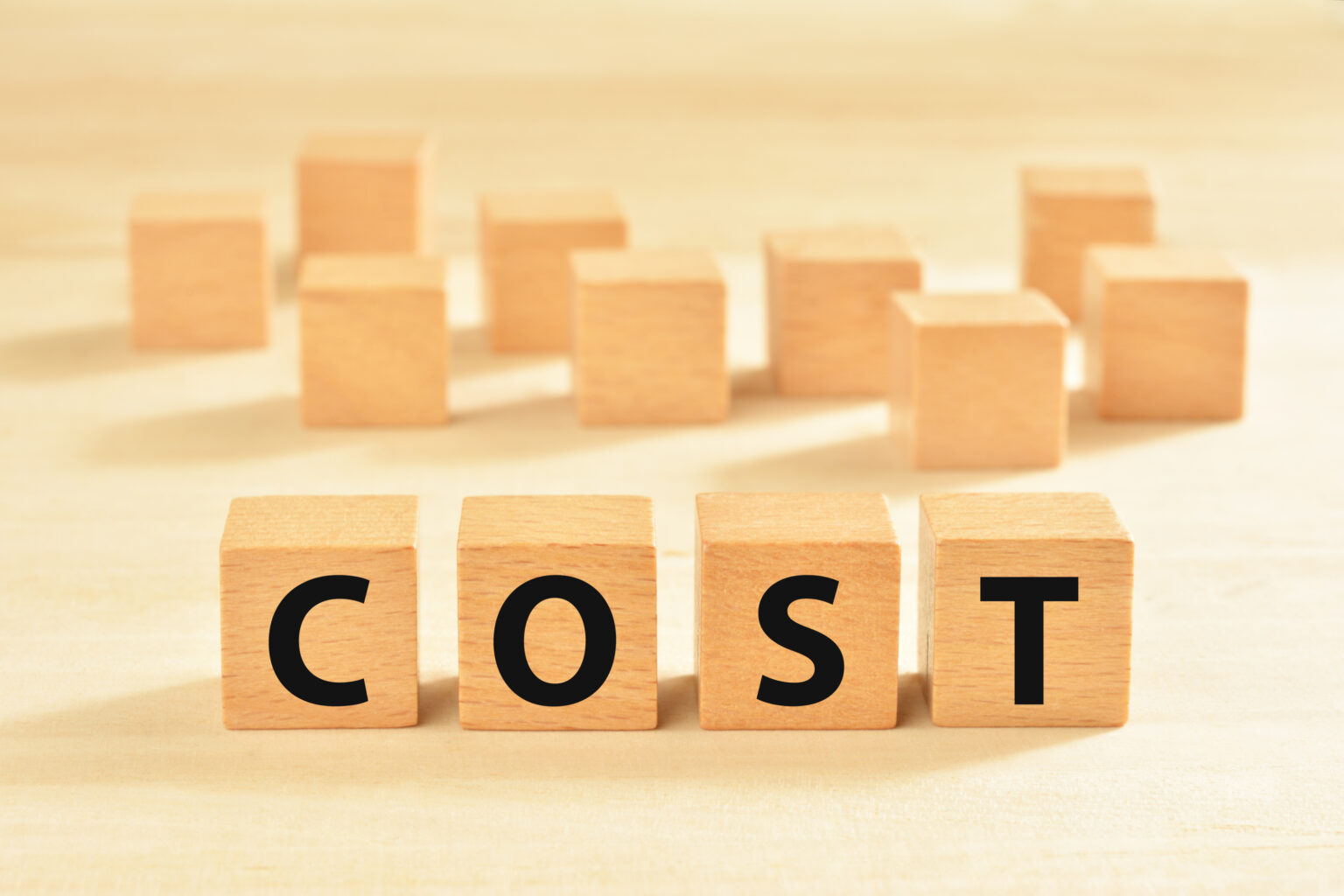
この記事は、以下のような方におすすめです。
鍛造についての基本的な知識を知りたい方。
鍛造費用を削減したいと思っている方。
コスト削減の方法やポイントを教えてほしい方。
鍛造を始める前に知っておくべきことを知りたい方。
もし、鍛造によって収入を得たいのであれば、鍛造費用削減方法を学ぶことが重要です。この記事では、鍛造における基本的な知識や費用削減の方法について詳しく紹介します。
多くの場合、鍛造には莫大なコストがかかりますが、この記事を通じて、効果的な鍛造費用削減のポイントを学ぶことで、より効率的に鍛造を行うことができるでしょう。
鍛造の世界に足を踏み入れる前に、この記事を読んで、鍛造費用削減のポイントを押さえましょう。
1. 鋳造から鍛造への切り替えによるコスト削減方法について知りたい
1-1. 鋳造と鍛造の違いとは?
鋳造と鍛造は、金属を形作る方法の一つですが、その違いがあります。
鋳造は、溶かした金属を型に流し込んで冷やし固める方法です。例えば、鋳物製の鍋やフライパンは、金属を溶かして型に流し込んで作られています。鋳造は大量生産が可能で、形状や複雑なデザインを作ることができます。
一方、鍛造は、金属を熱して叩いたり、圧力をかけて形を作る方法です。例えば、刃物や工具、自動車のエンジン部品などは、鍛造で作られています。鍛造は、金属の強度や耐久性を高めることができ、精密な形状を作ることも可能です。
つまり、鋳造は溶かして流し込む方法で、鍛造は熱して形を作る方法と言えます。どちらの方法も金属を形作るために重要な技術であり、さまざまな製品の製造に活用されています。
1-2. 鋳造から鍛造への切り替えによるコスト削減のメリットとは?
鋳造から鍛造への切り替えには、コスト削減のメリットがあります。鍛造は、金属を加熱して叩いたり圧縮したりして形を作る方法です。鋳造と比べると、鍛造はより強固で耐久性があります。また、鍛造によって材料の使用量を減らすことができ、コストを削減することができます。
鍛造は、材料を加熱して形を作るため、材料の強度を向上させることができます。そのため、同じ強度を持つ部品を作るためには、鋳造よりも少ない材料を使用することができます。これによって、材料の使用量を減らすことができ、コストを削減することができます。
また、鍛造は金属を圧縮することで形を作るため、より密度の高い部品を作ることができます。密度の高い部品は、より強固で耐久性があります。そのため、鍛造によって作られた部品は、長期間にわたって使用することができます。
鋳造から鍛造への切り替えによって、材料の使用量を減らし、より強固で耐久性のある部品を作ることができます。これによって、コストを削減することができます。鍛造は、製品の品質向上とコスト削減を同時に実現する方法です。
1-3. 鍛造への切り替えによるコスト削減の具体的な方法とは?
鍛造は、金属を加熱して柔らかくし、それから圧力をかけて形状を作り出す製造方法です。鍛造は、様々な産業で使用されており、自動車や航空機などの製造に欠かせない技術です。
鍛造には、他の製造方法と比べてコスト削減のメリットがあります。具体的な方法としては、以下の5つのポイントが挙げられます。
- 材料の効率的な利用: 鍛造では、材料を正確に必要な形状に加工することができます。これにより、材料の無駄を減らすことができます。
- 加工時間の短縮: 鍛造は、一度に多くの製品を作ることができるため、加工時間を短縮することができます。これにより、生産効率を向上させることができます。
- 機械の利用: 鍛造には、特別な機械が必要ですが、一度導入すれば長期間使用することができます。そのため、機械のコストを均等に分散させることができます。
- 品質の向上: 鍛造は、材料の密度を高めることができるため、製品の強度や耐久性を向上させることができます。これにより、製品の品質を高めることができます。
- 再利用の可能性: 鍛造で作られた製品は、再利用することができます。例えば、廃棄物のリサイクルや修理など、さまざまな方法で再利用することができます。
これらのポイントを考慮しながら、鍛造を活用することで、コスト削減を実現することができます。鍛造は、効果的な製造方法として、今後もさらに注目を集めるでしょう。
2. 削出し機械加工から鍛造への切り替えによるコスト削減方法について知りたい
2-1. 削出し機械加工と鍛造の違いとは?
削出し機械加工と鍛造は、金属を形作るための二つの異なる方法です。
まず、削出し機械加工について説明しましょう。削出し機械加工は、金属を削り取って形を作る方法です。これは、金属を切削工具で削り取ることによって、所望の形状を作り出します。この方法は、CNC(コンピュータ数値制御)機械を使用して自動的に行われることが多く、高い精度で作業が行われます。削出し機械加工は、さまざまな形状や複雑なデザインを作り出すことができますが、材料のロスが発生しやすく、時間とコストがかかることが欠点です。
一方、鍛造は、金属を加熱して形を作る方法です。金属を加熱することによって、材料が柔らかくなり、ハンマーやプレスなどの工具を使って形状を作り出します。鍛造は、金属の結晶構造を変えることによって、強度や耐久性を向上させることができます。また、鍛造によって材料のロスを最小限に抑えることができ、高い品質と効率性を実現できます。
削出し機械加工と鍛造は、それぞれ異なる特徴と利点を持っています。どちらの方法が最適かは、使用する材料や形状によって異なる場合があります。
2-2. 削出し機械加工から鍛造への切り替えによるコスト削減のメリットとは?
鍛造は、金属を加熱して叩いたり圧縮したりして形を作り出す技術です。削出し機械加工と比べると、鍛造は一度に多くの製品を作ることができるため、効率的な生産が可能です。
鍛造によるコスト削減のメリットはいくつかあります。まず、材料の使用量が少なくて済むため、材料費が削減されます。また、鍛造によって作られた製品は耐久性が高く、強度もあります。そのため、製品の寿命が長くなり、修理や交換のコストも削減できます。
さらに、鍛造は形状が複雑な製品を作ることも可能です。これにより、部品の数を減らすことができ、組み立て作業の手間や時間を削減できます。また、鍛造によって作られた製品は、精度が高く、仕上がりも美しいです。
鍛造はコスト削減に効果的な方法です。鍛造を活用することで、製品の品質を向上させながら、コストを抑えることができます。
2-3. 鍛造への切り替えによるコスト削減の具体的な方法とは?
鍛造は、金属を熱して叩いたり圧縮したりすることで形状を作り出す技術です。鍛造は、製品の強度や耐久性を向上させることができるだけでなく、材料の無駄を減らすこともできます。では、鍛造のコストを抑えるためにはどうすればよいのでしょうか?
まず、一つ目のポイントは、設計の最適化です。製品の設計を最初から鍛造に適した形状にすることで、材料の無駄を減らすことができます。例えば、穴や溝を鍛造品に組み込むことで、後から加工する必要がなくなります。
二つ目のポイントは、鍛造の工程を効率化することです。鍛造は、材料を熱して叩いたり圧縮したりするため、工程が複雑になりがちです。しかし、工程を簡略化することで、製造時間や人件費を削減することができます。
三つ目のポイントは、材料の選択です。鍛造には、さまざまな種類の金属が使われますが、コストを抑えるためには適切な材料を選ぶことが重要です。材料の価格や特性を比較し、最もコスト効率の良いものを選びましょう。
四つ目のポイントは、生産量の増加です。鍛造は、一度に多くの製品を作ることができるため、生産量を増やすことで単位あたりのコストを下げることができます。需要の見込みや販売計画を考慮し、効率的な生産体制を整えましょう。
最後のポイントは、技術の向上です。鍛造技術は日々進歩していますので、最新の技術を導入することで効率化や品質向上が図れます。定期的に技術の研究や改善を行い、競争力を維持しましょう。
以上が、鍛造のコスト削減のポイントです。設計の最適化や工程の効率化、材料の選択、生産量の増加、技術の向上という5つのポイントを意識することで、鍛造コストを抑えることができます。
3. 工法転換による冷間鍛造のメリットについて詳しく知りたい
3-1. 冷間鍛造と他の鍛造方法の違いとは?
冷間鍛造は、金属を加熱せずに行われる鍛造方法です。他の鍛造方法との違いは、材料の温度です。冷間鍛造では、金属材料が室温のままで使用されます。
冷間鍛造のメリットは、材料の強度や硬度が高くなることです。また、材料の変形が少なく、精度の高い製品を作ることができます。さらに、冷間鍛造では余分な材料の使用を抑えることができるため、コスト削減にもつながります。
一方、冷間鍛造のデメリットは、材料の加工性が低下することです。冷間鍛造では、材料の硬さや脆さが増すため、加工が難しくなります。また、冷間鍛造には専用の機械や設備が必要であり、初期投資が必要となる場合もあります。
冷間鍛造は、自動車や航空機などの産業で広く使用されています。高い強度や精度が求められる部品の製造に適しており、品質の向上やコスト削減に貢献しています。
3-2. 工法転換による冷間鍛造のメリットとは?
冷間鍛造は、鍛造の方法の一つであり、鉄やアルミニウムなどの金属を加熱せずに鍛造する技術です。冷間鍛造には、いくつかのメリットがあります。
まず、冷間鍛造は熱を使わないため、エネルギー消費が少なくなります。熱を使わないことで、鍛造に必要なエネルギーのコストを削減することができます。また、熱を加えないため、鍛造品の品質も安定しています。
さらに、冷間鍛造は材料の節約にもつながります。熱を加えずに鍛造するため、材料が無駄になることがありません。これにより、鍛造に使用する材料のコストを削減することができます。
また、冷間鍛造は精度が高いという特徴もあります。熱を使わないため、鍛造品の形状や寸法を正確に制御することができます。これにより、高品質な製品を生産することができます。
冷間鍛造は、鍛造コストを抑えるための効果的な方法の一つです。エネルギー消費の削減や材料の節約、高い精度などのメリットがあります。これらのポイントを抑えることで、鍛造業界での競争力を高めることができます。
3-3. 冷間鍛造の具体的な事例と成功事例について知りたい
冷間鍛造は、金属を加熱せずに成形する鍛造方法です。この方法は、鋼材やアルミニウムなどの金属をより強く、耐久性のある形状にするために使用されます。
冷間鍛造の具体的な事例としては、自動車部品や工具、建築資材などがあります。自動車部品では、エンジンのクランクシャフトやサスペンションのアームなどが冷間鍛造で作られています。これにより、軽量化や強度の向上が実現され、車両の性能が向上します。
また、工具や建築資材においても、冷間鍛造は広く利用されています。例えば、ハンマーやドリルビットなどの工具は、冷間鍛造によって強度が高くなり、長持ちします。建築資材では、鋼材を冷間鍛造して作られた構造部材は、強度が増し、建物の安全性が向上します。
冷間鍛造は、金属の特性を最大限に活かすことができる方法です。そのため、耐久性や強度が求められる製品や部品の製造に適しています。成功事例としては、日本の自動車メーカーや建築資材メーカーが冷間鍛造を積極的に活用しており、高品質な製品を提供しています。
4. 鋳造部品から鍛造部品への変更によるコストダウン方法について知りたい
4-1. 鋳造部品と鍛造部品の違いとは?
鋳造部品と鍛造部品は、どちらも製造工程で使用される部品ですが、その製造方法や特徴には違いがあります。
まず、鋳造部品は、溶けた金属を型に流し込んで作られます。この方法では、金属を溶かして流し込むだけなので、複雑な形状や細部まで再現することができます。また、大量生産が可能であり、比較的安価に製造することができます。しかし、鋳造部品は内部に気泡や不純物が含まれることがあるため、強度や耐久性にはやや難があります。
一方、鍛造部品は、金属を加熱して叩いたり圧縮したりして形成されます。この方法では、金属の結晶構造を整えることができるため、強度や耐久性が高くなります。また、鍛造部品は一つ一つ手作業で作られるため、細部まで丁寧に仕上げることができます。しかし、製造には時間と手間がかかり、コストも高くなります。
したがって、鋳造部品は大量生産や複雑な形状が求められる場合に適しており、鍛造部品は強度や耐久性が重要な場合に適しています。どちらの部品も、その特徴を理解して適切に使用することが重要です。
4-2. 鋳造部品から鍛造部品への変更によるコストダウンのメリットとは?
鋳造部品から鍛造部品への変更には、コストダウンのメリットがあります。
まず、鍛造部品は鋳造部品と比べて、強度や耐久性が高いという特徴があります。これは、鍛造部品が高温で圧力をかけて形成されるため、内部の結晶構造が整い、強い結合力を持つからです。そのため、同じ材料でも鍛造部品の方がより頑丈で長持ちします。
また、鍛造部品は形状の自由度が高く、複雑な形状や細かいディテールを実現することができます。これにより、鋳造部品では難しかった設計上の制約を解消し、より効率的な部品を作ることができます。
さらに、鍛造部品は加工の手間が少なく、材料のロスも少ないという利点があります。鋳造部品では冷却や仕上げ加工が必要ですが、鍛造部品はそのような作業が不要です。そのため、生産効率が向上し、コストを削減することができます。
鋳造部品から鍛造部品への変更は、強度や耐久性の向上、設計の自由度、加工の簡素化など、さまざまなメリットをもたらします。これにより、製品の品質向上とコスト削減を同時に実現することができます。
4-3. 鋳造部品から鍛造部品への変更の具体的な方法とは?
鋳造部品から鍛造部品への変更をするためには、いくつかの具体的な方法があります。
まず、鋳造部品の設計を見直すことが重要です。鍛造部品は、鋳造部品よりも強度が高く、耐久性に優れています。そのため、鍛造部品に変更する際には、設計を再考し、必要な強度や耐久性を確保するようにすることが大切です。
次に、材料の選定を見直すことも必要です。鍛造部品は、鋳造部品よりも材料の性能が求められます。より強度の高い材料を使用することで、鍛造部品の品質を向上させることができます。
また、製造プロセスの見直しも重要です。鍛造部品は、鋳造部品と比べて製造工程が複雑ですが、その分品質も高くなります。製造プロセスを最適化し、効率的に生産することで、鍛造部品のコストを抑えることができます。
さらに、協力会社との連携も重要です。鍛造部品の製造は、専門的な技術や設備が必要です。協力会社との良好な関係を築き、技術やノウハウを共有することで、鍛造部品の品質とコストを向上させることができます。
計画的な部品の在庫管理も大切です。鍛造部品は、製造に時間がかかるため、在庫管理が重要です。適切な在庫管理を行うことで、生産効率を向上させることができます。
以上が、鋳造部品から鍛造部品への変更の具体的な方法です。これらのポイントを抑えることで、鍛造部品の品質向上とコスト削減を実現することができます。
まとめ
この記事では、鍛造に関心のある読者が抱える悩みや疑問に対して、鋳造から鍛造への切り替えや削出し機械加工から鍛造への切り替えによるコスト削減方法、工法転換による冷間鍛造のメリット、鋳造部品から鍛造部品への変更によるコストダウン方法について解説します。これらの情報を参考にして、鍛造によるコスト削減の可能性を探ってみてください。
鍛造コストを抑える方法には以下の5つのポイントがあります。1つ目は設計の最適化で、無駄な部品や加工を省くことが大切です。2つ目は素材の選定で、コストと性能のバランスを考えましょう。3つ目は生産効率の向上で、工程の見直しや自動化を検討しましょう。4つ目は供給チェーンの最適化で、素材や部品の調達を効率化します。最後に5つ目は鍛造プロセスの改善で、工具や設備の最適化を行います。これらのポイントを組み合わせることで鍛造費用の削減が可能です。