金属加工の表面粗さに関する基本知識とは?効果的な方法を解説
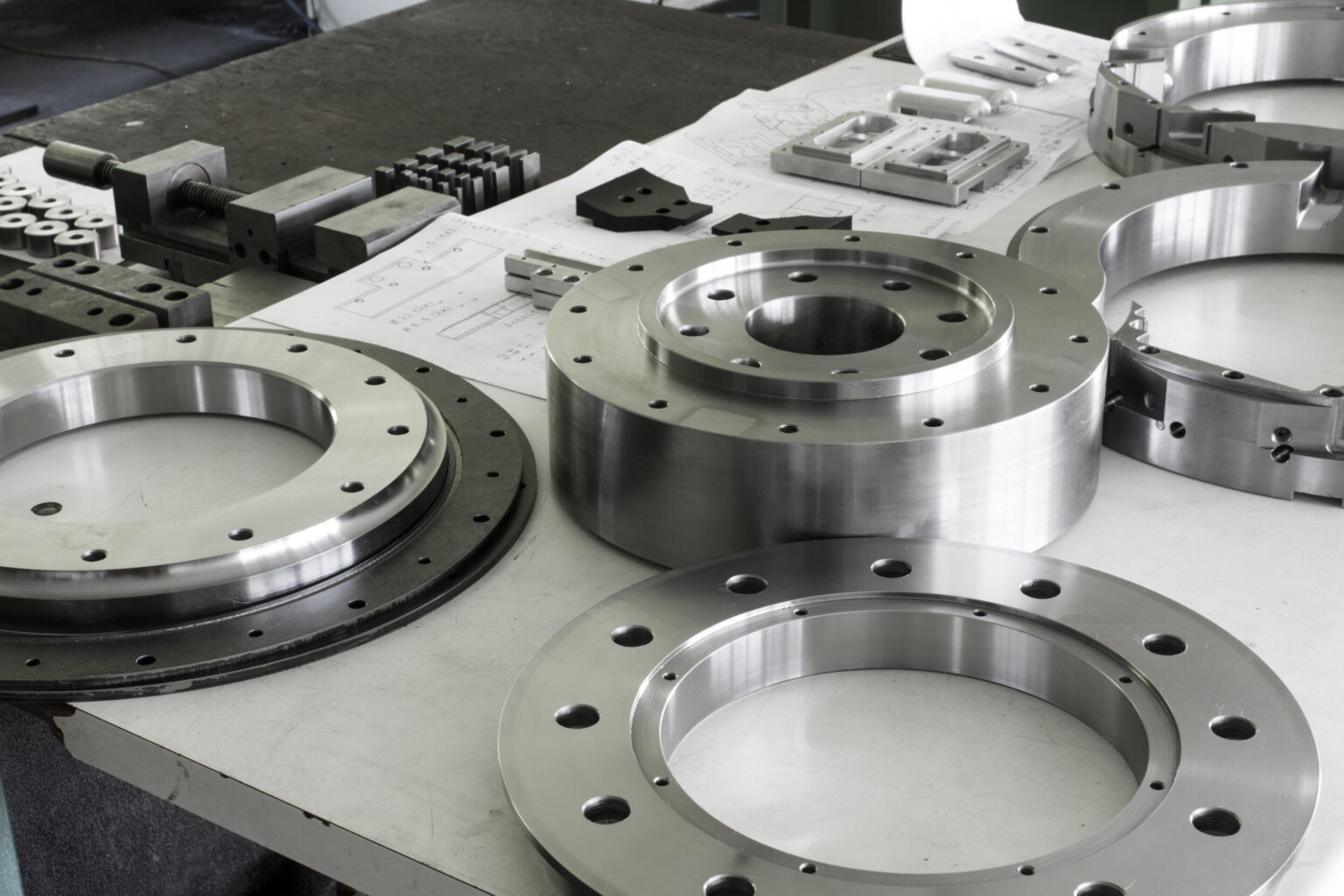
表面粗さは、金属加工において非常に重要な要素です。なぜなら、表面粗さが十分でないと、製品の耐久性や外観に大きな影響を与えるからです。
本記事では、金属加工の表面粗さに関する基本知識を解説します。また、効果的な方法や注意点についても詳しくご紹介します。
金属加工に関わる方々にとって、表面粗さの理解は製品の品質向上に繋がります。是非、この記事を通じて基礎知識を深め、より効果的な金属加工を実現してください。
1. 表面粗さの書き方に関する悩み
1-1. 表面粗さの定義とは?
金属加工において、表面粗さとは、金属の加工が終わった後の表面の粗さのことを指します。表面粗さは、加工した金属の品質や機能に直接影響を与える重要な要素です。
表面粗さは、一般的にはマイクロメートル(μm)単位で表されます。表面が滑らかであるほど、表面粗さは小さくなります。一方、表面がザラザラしていると、表面粗さは大きくなります。
表面粗さの測定方法には、さまざまな手法があります。代表的な方法としては、表面を触って感じる方法や、専用の測定器を使用する方法があります。また、表面粗さの測定結果は、数値やグラフで表されることが一般的です。
表面粗さの適切な管理は、金属製品の品質や機能を向上させるために重要です。例えば、自動車のエンジン部品や航空機の部品など、高い精度が求められる製品では、表面粗さの管理が特に重要となります。
金属加工においては、表面粗さを適切に制御するためのさまざまな方法があります。例えば、切削工具の適切な選択や、加工条件の最適化などが挙げられます。
表面粗さの基本知識を理解することは、金属加工において高品質な製品を作るために欠かせません。今後も金属加工技術の進化に伴い、より精度の高い表面粗さの管理が求められることでしょう。
1-2. 表面粗さの測定方法と手法
金属加工において、表面粗さの測定は非常に重要な要素です。表面粗さは、加工された金属の滑らかさや品質を示す指標となります。では、表面粗さを測定する方法と手法について見ていきましょう。
まず、表面粗さを測定するためには、専用の測定器具が必要です。一般的に使用される測定器具には、表面粗さ計やプロファイル計があります。これらの器具は、金属の表面に触れて測定を行います。
測定手法としては、主に3つの方法があります。一つ目は、切削法です。これは、金属の表面に切削工具を使用して測定を行う方法です。切削工具の刃先が金属の表面をなぞることで、表面の凹凸を測定します。
二つ目は、光学法です。この方法では、光を金属の表面に照射し、反射された光のパターンを観察します。このパターンから、表面の凹凸を測定することができます。
三つ目は、触覚法です。この方法では、金属の表面に触覚センサーを使用して測定を行います。触覚センサーが表面の凹凸を感知し、その情報を測定器具に送ります。
以上が、金属加工における表面粗さの測定方法と手法の基本知識です。これらの方法を適切に使用することで、金属加工の品質管理や改善に役立てることができます。
1-3. 表面粗さの数値表現と単位
金属加工において、表面粗さは非常に重要な要素です。表面粗さは、金属の加工品の仕上がりや品質に大きな影響を与えるため、正確な数値表現が必要です。
表面粗さは、通常、Ra(中心線平均粗さ)やRz(十点平均粗さ)といった数値で表されます。Raは、加工品の表面の凹凸を示す指標であり、数値が小さいほど表面が滑らかであることを意味します。一方、Rzは表面の高低差を示し、数値が大きいほど表面が粗いことを意味します。
これらの数値は、一般的にマイクロメートル(μm)やナノメートル(nm)といった単位で表されます。例えば、Raが0.1μmの場合、表面は非常に滑らかであり、0.5μmの場合はやや粗い表面となります。
表面粗さの数値表現は、金属加工業界で共通の基準となっており、品質管理や加工条件の設定に役立ちます。また、顧客の要求に応じた表面粗さを実現するために、適切な加工方法や工具の選択が重要です。
金属加工において、表面粗さの理解と適切な数値表現は、品質向上や製品競争力の向上につながります。今後も金属加工業界では、さらなる表面粗さの研究や改善が進められることが期待されます。
2. 切削加工における表面粗さの理解に関する悩み
2-1. 切削加工による表面粗さの影響
金属加工において、切削加工は一般的な方法です。切削加工では、工具を使って金属を削り取ることで形を作ります。しかし、切削加工によって生じる表面粗さは、そのままでは使用できない場合があります。
切削加工による表面粗さは、加工条件や使用する工具の種類によって異なります。例えば、切削速度や切削量が大きいほど、表面は粗くなります。また、刃先の状態や刃先の角度も表面粗さに影響を与えます。
表面粗さが大きいと、摩擦が増えて摩耗が進んだり、外観が悪くなったりすることがあります。そのため、表面粗さを適切に管理することは重要です。
表面粗さを改善する方法として、切削条件の最適化や工具の選定があります。切削条件の最適化では、切削速度や切削量を調整して表面粗さを制御します。また、工具の選定では、刃先の形状や材質を適切に選ぶことで、表面粗さを改善することができます。
金属加工において、表面粗さは品質や性能に大きな影響を与える要素です。適切な切削条件や工具の選定によって、高品質な加工品を作ることができます。
2-2. 切削条件と表面粗さの関係
切削条件と表面粗さには密接な関係があります。切削条件とは、切削速度、送り速度、切削量などのパラメーターのことを指します。これらの条件が変化すると、加工される金属の表面の粗さにも変化が生じます。
切削速度が速い場合、切削による熱が金属に与える影響が大きくなります。その結果、金属の表面が溶けたり、剥がれたりすることがあります。一方、切削速度が遅い場合、金属の表面に切削痕が残りやすくなります。
送り速度が大きい場合、切削による摩擦が増えます。これによって金属の表面が損傷しやすくなります。一方、送り速度が小さい場合、切削痕が細かくなり、表面の粗さが減少します。
また、切削量も表面粗さに影響を与えます。切削量が大きい場合、金属表面に大きな切削痕が残り、表面の粗さが増加します。切削量が小さい場合、切削痕が細かくなり、表面の粗さが減少します。
したがって、金属加工においては、適切な切削条件を選ぶことが重要です。切削条件を適切に設定することで、金属の表面粗さをコントロールすることができます。
2-3. 切削加工における表面仕上げの方法
金属加工において、切削加工による表面仕上げは非常に重要です。表面仕上げは、製品の見た目や性能に大きな影響を与えるため、品質向上に欠かせません。
切削加工における表面仕上げの方法には、いくつかの種類があります。まず、最も一般的な方法として、研磨があります。研磨は、研磨剤を使用して表面を滑らかにする方法であり、鏡面仕上げなどの高品質な仕上げが可能です。
また、バフ研磨と呼ばれる方法もあります。バフ研磨は、布を使用して表面を磨く方法であり、光沢感のある仕上げが得られます。
さらに、研削と呼ばれる方法もあります。研削は、砥石を使用して表面を削る方法であり、精度の高い仕上げが可能です。
これらの方法は、加工する金属の種類や形状によって適切な方法を選ぶ必要があります。また、表面仕上げの目的や要件にも応じて、適切な方法を選ぶことが重要です。
金属加工における表面仕上げは、製品の品質を向上させるだけでなく、見た目や耐久性にも大きな影響を与えます。適切な方法を選び、丁寧に表面を仕上げることで、高品質な製品を作り上げることができます。
3. 表面粗さの種類や表面記号、仕上げ記号に関する悩み
3-1. 表面粗さの種類と特徴
金属加工において、表面粗さは非常に重要な要素です。表面粗さは、加工された金属の外観や性能に大きな影響を与えるため、正確な測定と適切な管理が必要です。
表面粗さは、一般的に次の3つの種類に分類されます。
- ラフネス(粗さ):表面の凹凸や凹凸の深さを測定する指標です。この指標は、金属の摩擦や耐久性に影響を与えます。例えば、自動車のエンジン部品の表面粗さが適切でないと、摩擦が増加し、機械的な故障や劣化が起こる可能性があります。
- 波状度(ワベ):表面の波状の特性を測定する指標です。金属の表面が滑らかであるほど、摩擦が減少し、機械的な動作がスムーズになります。例えば、高速回転する軸受け部品の表面粗さが適切でないと、回転の安定性や効率が低下する可能性があります。
- 輝度(光沢):表面の光沢や反射能力を測定する指標です。金属の表面が光沢を持つほど、製品の見た目や美しさが向上します。例えば、家電製品や装飾品の表面粗さが適切でないと、顧客の満足度が低下する可能性があります。
これらの表面粗さの種類は、金属加工の目的や要件に応じて適切に管理する必要があります。正確な測定と適切な加工技術の選択により、金属製品の品質や性能を向上させることができます。
3-2. 表面記号と仕上げ記号の意味と使い方
金属加工において、表面粗さは非常に重要な要素です。表面粗さは、加工された金属の表面の平滑さや凹凸の程度を示す指標です。表面粗さの値が大きいほど、表面が粗いことを意味します。
表面粗さは、金属加工において望ましい仕上がりを得るために考慮しなければならない要素です。例えば、機械部品の摩擦抵抗を減らすためには、表面粗さを小さくする必要があります。また、塗装やめっきなどの表面処理を行う場合にも、表面粗さの値を制御することが重要です。
表面粗さは、ISO(国際標準化機構)によって規定された表面記号と仕上げ記号によって表されます。表面記号は、表面粗さの値を表し、仕上げ記号は、加工方法や仕上げの状態を表します。
例えば、表面記号の一つであるRaは、表面の平均粗さを示す値です。Raの値が小さいほど、表面は滑らかです。また、仕上げ記号の一つであるBは、バフ研磨を行ったことを示します。
金属加工においては、適切な表面粗さを選ぶことが重要です。使用する金属や加工目的に応じて、適切な表面粗さを選択しましょう。
3-3. 表面粗さの指定方法と注意点
金属加工において、表面粗さは非常に重要な要素です。表面粗さは、加工された金属の外観や機能に大きな影響を与えます。では、表面粗さを指定する方法とその注意点について見ていきましょう。
まず、表面粗さを指定する方法ですが、一般的には「Ra値」という指標が使われます。Ra値は、表面の凹凸の平均値を示すものであり、小さいほど表面が滑らかであることを意味します。一般的な金属加工では、Ra値が0.1μm以下であることが求められます。
次に、表面粗さの注意点です。まず、加工方法によって表面粗さが異なることがあります。例えば、切削加工や研磨加工など、異なる方法で加工された金属の表面粗さは異なる場合があります。また、金属の種類によっても表面粗さは変わることがあります。
さらに、金属の用途によっても表面粗さの指定は異なります。例えば、機械部品などの摩擦が生じる場所では、表面粗さを小さくすることが求められます。一方、塗装などの表面処理を行う場合には、適切な表面粗さを保つことが重要です。
金属加工において、適切な表面粗さを指定することは製品の品質や耐久性に直結します。加工業者とのコミュニケーションをしっかりと行い、目的に応じた表面粗さを実現することが大切です。
4. 表面粗さや面粗度の基礎知識に関する悩み
4-1. 表面粗さと面粗度の違いと関係
金属加工において、表面粗さと面粗度という2つの指標がありますが、これらは異なる意味を持ちます。
まず、表面粗さは、金属の表面のざらつきや滑らかさを表す指標です。表面が粗いほど、ざらざらしていて滑りにくくなります。一方、表面が滑らかであれば、指やツールがスムーズに動かせます。表面粗さは、加工方法や材料の性質によって異なる値を示します。
一方、面粗度は、金属の表面の平坦さや均一さを表す指標です。面粗度が高いほど、表面が凹凸していて平坦さに欠けます。面粗度が低いほど、表面が均一で平坦です。面粗度は、加工方法や加工精度によって異なる値を示します。
表面粗さと面粗度は、金属加工において重要な要素です。例えば、自動車のエンジン部品や航空機の部品など、正確な加工が求められる場合には、表面粗さや面粗度を制御する必要があります。また、金属の塗装や接着などの処理を行う場合にも、表面粗さや面粗度が影響を与えることがあります。
金属加工においては、表面粗さと面粗度を適切に制御することが重要です。加工方法や材料の選択、加工精度の向上など、様々な方法があります。適切な表面粗さや面粗度を実現することで、金属製品の品質や性能を向上させることができます。
4-2. 表面粗さの測定結果の解釈方法
金属加工において、表面粗さの測定結果を正しく解釈することは非常に重要です。表面粗さは、加工された金属の表面の凹凸や滑らかさを示す指標です。
まず、表面粗さの数値が小さい場合、金属の表面は滑らかであり、凹凸が少ないことを意味します。一方、数値が大きい場合は、表面に凹凸があり、粗いことを示します。
表面粗さの測定結果を解釈する際には、比較対象が重要です。例えば、同じ材料を使用している場合でも、加工方法や加工条件が異なれば、表面粗さは変わることがあります。したがって、比較対象となる基準を設けることが重要です。
さらに、表面粗さの測定結果を具体的な例で説明します。例えば、自動車のエンジン部品の表面粗さが大きい場合、潤滑油の保持力が低下し、摩擦が増える可能性があります。その結果、エンジンの性能が低下する可能性があります。
金属加工における表面粗さの測定結果は、金属の品質や性能に大きく影響を与える重要な要素です。正確な測定と適切な解釈を行うことで、金属加工の品質向上や問題の早期発見につながります。
4-3. 表面粗さの許容範囲と品質基準
金属加工において、表面粗さは非常に重要な要素です。表面粗さが適切でないと、製品の品質や機能に悪影響を及ぼす可能性があります。そのため、金属加工における表面粗さの許容範囲や品質基準を理解することは重要です。
表面粗さの許容範囲は、その金属加工の用途や要件によって異なります。例えば、自動車のエンジン部品や航空機の部品など、高精度な加工が求められる場合は、表面粗さの許容範囲が非常に狭くなります。一方、建築用の金属材料や一般的な機械部品など、精度がそれほど求められない場合は、許容範囲が広くなります。
品質基準は、表面粗さの測定方法や基準値に基づいています。一般的には、表面粗さを測定するための測定器具や規格が使用されます。測定結果が基準値に適合していれば、その製品は品質基準を満たしているとされます。
金属加工における表面粗さの許容範囲と品質基準を守るためには、適切な加工技術や測定方法を使用することが重要です。また、製品の用途や要件に応じて、適切な表面粗さの設定を行うことも重要です。
金属加工の表面粗さに関する基本知識を理解し、効果的な方法を実践することで、高品質な製品を生み出すことができます。金属加工業界において、表面粗さの管理は欠かせない要素となっています。
5. 設計者が知っておくべき表面粗さの重要性に関する悩み
5-1. 設計段階での表面粗さの考慮ポイント
金属加工において、製品の品質や性能を左右する重要な要素の一つが表面粗さです。製品の設計段階で表面粗さを考慮することは、製品の寿命や機能に直結するため非常に重要です。
まず、設計段階での表面粗さの考慮ポイントとして、製品の用途や要求される性能に応じた適切な表面粗さを設定することが挙げられます。例えば、機械部品の場合は摩擦や摩耗の影響を受けるため、適切な表面粗さを設定することが必要です。
また、製品の材料によっても表面粗さの設定が異なります。材料の硬さや耐久性によって、表面粗さの設定が変わることがあります。例えば、柔らかい材料の場合は表面粗さを細かくすることで摩擦を軽減することができます。
さらに、製品の加工方法や加工工程によっても表面粗さは変わります。加工工程においては、切削や研磨などの方法を適切に選択することで、求められる表面粗さを実現することができます。
設計段階での表面粗さの考慮は、製品の品質や性能に大きな影響を与えるため、十分な注意が必要です。適切な表面粗さの設定を行うことで、製品の寿命や機能を向上させることができます。
5-2. 表面粗さが品質や機能に与える影響
金属加工において、表面粗さは品質や機能に大きな影響を与えます。表面粗さが適切でないと、製品の性能や耐久性が低下し、見た目の美しさも損なわれる可能性があります。
まず、品質への影響について考えてみましょう。金属製品の表面粗さが大きいと、摩擦や摩耗が増加し、製品の寿命が短くなる可能性があります。また、表面粗さが均一でないと、製品の強度や剛性にも影響を与えることがあります。そのため、金属加工においては、表面粗さを適切に管理することが重要です。
次に、機能への影響について考えてみましょう。金属製品の表面粗さは、接合や密着性にも関与します。表面が滑らかであれば、接合部や密着部の強度が高まりますが、表面が粗い場合は、接合や密着がうまくいかず、製品の機能に支障をきたすことがあります。
具体的な例を挙げると、自動車のエンジン部品や航空機の部品など、高い精度と品質が求められる製品では、表面粗さの管理が非常に重要です。また、美しい仕上がりが求められる装飾品や家具などでも、表面粗さに気を配る必要があります。
金属加工においては、表面粗さの適切な管理が品質や機能に大きな影響を与えることがわかりました。製品の寿命や性能を向上させるためにも、金属加工業者や製造業者は表面粗さに注意を払う必要があります。
5-3. 表面粗さの最適化と改善方法
金属加工において、表面粗さの最適化と改善は非常に重要です。なぜなら、金属の表面粗さが適切でないと、製品の品質や性能に影響を及ぼす可能性があるからです。
まず、表面粗さの最適化の理由を考えてみましょう。金属の表面は、加工方法や材料の種類によって異なる粗さとなります。適切な表面粗さを実現することで、製品の寿命や耐久性を向上させることができます。また、摩擦や摩耗の抵抗力も向上させることができます。
さらに、表面粗さの改善方法についても考えてみましょう。一つの方法は、加工工程での切削や研磨を行うことです。切削によって表面を削り、研磨によって滑らかな表面を作り出すことができます。また、化学処理や熱処理などの特殊な方法もあります。
具体的な例を挙げると、自動車のエンジン部品や航空機のタービン部品など、高精度な金属製品では表面粗さの最適化が重要です。これらの製品は高い性能を求められるため、表面粗さの最適化を行うことで、製品の品質と性能を向上させることができます。
まとめると、金属加工においては表面粗さの最適化と改善が重要であり、適切な表面粗さを実現することで製品の品質や性能を向上させることができます。特に高精度な製品では、表面粗さの最適化がより重要となります。
まとめ
金属加工の表面粗さは、製品の品質や機能に大きな影響を与えます。表面粗さを測定するための基本的なパラメーターには、RaやRzなどがあります。効果的な方法としては、研削や研磨、サンドブラストなどの手法があります。また、適切な工具や研磨材料の選択、適切な加工条件の設定も重要です。これらの方法を適切に組み合わせることで、高品質な表面仕上げが可能となります。